5 Key Technologies for Industry 4.0
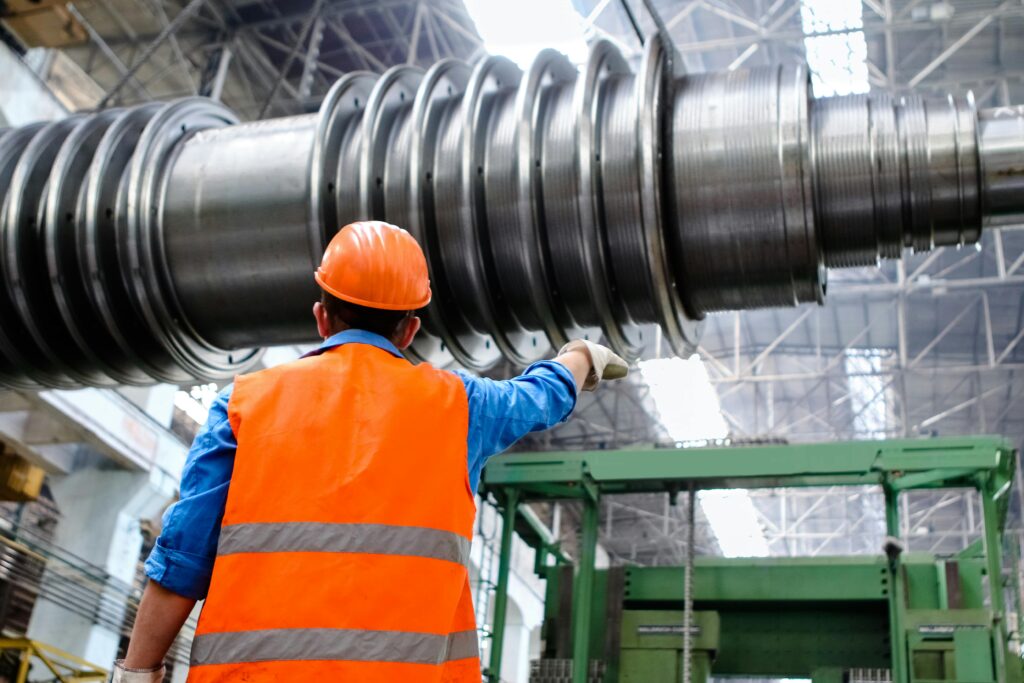
The Internet of Things, big data and analytics, cloud computing, cyber-physical systems and augmented reality are foundational technologies for Industry 4.0.
Companies are adopting Industry 4.0 technologies at a furious pace as they seek to gain promised benefits including improved productivity, greater business intelligence, and lower costs. But what, exactly, are the key technologies underpinning Industry 4.0?
That was the question I set out to answer for this post, and there’s certainly no shortage of opinions on the topic. I scoured dozens of blog posts and research from pundits and actual players in the market. Drawing on that, as well as my own 30+ years of experience covering IT topics, I came up with the five described below.
Before we get to the list, I’m using the term Industry 4.0 as synonymous with the “fourth industrial revolution,” meaning it applies to any industry, not just manufacturing. While purists will say (with some justification) that “Industry 4.0” only applies to manufacturing, it’s just so much less of a mouthful than “fourth industrial revolution,” so I’m running with it.
With that out of the way, here’s the list.
-
Internet of Things
Internet of Things (IoT), as well as Industrial IoT technology, is fundamental to any Industry 4.0 effort. The whole Industry 4.0 concept requires the collection of data from all sorts of devices and sensors, whether machines in a manufacturing plant, sensors spread throughout a farm, or devices in a hospital. Collecting data is what IoT is all about.
-
Big Data and Analytics
Collecting data is just one piece of the puzzle. The next step is to put it all into a database or data lake and apply analytics to create actionable business intelligence. The more data you have, the better the intelligence will be—hence, big data. Artificial intelligence and machine learning (AI/ML) also play into this, of course, as they do in No. 4. (See below.)
-
Cloud Computing
Running these AI/ML applications requires significant compute power and expertise, which most companies don’t have in-house and would rather not build. There’s no need to, really, when they can turn to any number of cloud computing providers to supply those resources for them, at more affordable rates.
-
Cyber-physical Systems
Cyber-physical systems (CPS) is where Industry 4.0 technology gets really interesting. As described by UC Berkeley, CPS are “integrations of computation, networking, and physical processes.” Here’s a good description of what it’s all about, from OTTO Motors, which makes autonomous vehicles: “Computers and networks monitor and control physical processes with feedback loops; the physical system reacts, the system uses software to interpret the action and tracks results. The notion centers on computers and software being embedded in devices where the first use is not computation; rather it is a loop of action and machine learning.” The concept is still in its early phases but holds the promise of taking AI/ML to new levels.
-
Augmented Reality
Augmented reality is likewise still in early stages, but it’s being used in all sorts of industries with benefits that are easy to see. Think about a technician in the field, trying to repair a machine. With AR, he can “see” exactly what’s wrong and get instructions on how to perform the repair. It’s not hard to envision the technology being employed in areas as diverse as healthcare and education to manufacturing. As researchers at BCG put it, “In the future, companies will make much broader use of augmented reality to provide workers with real-time information to improve decision making and work procedures.”
Plenty of other technologies have a role in Industry 4.0. Had I been focusing on manufacturing, I certainly would’ve included robots and cobots (collaborative robots) and “additive manufacturing,” which includes 3D printing. But the above list can and should apply to most any Industry 4.0 application.